手はんだ付は、あらゆる電子機器メーカーのオタクスキルのレパートリーにおいて、象徴的な技能のひとつであると思われています。はんだ付はロケット科学ではありません。初心者にとっては面白いイベントになるかもしれません。ちゃんと練習すれば簡単に身につけるようになるかもしれません。
でも、PCBに半田投げることができると言っても、品質があるかは別問題です。部品の小型化とコンパクト化に伴い、はんだ付の問題が発生する可能性が高くなっています。PCBAの品質がよいかどうかは 、PCBに半田投げる品質で決まります。

そこで、自宅で行われるプロジェクトで様々なはんだ付の問題を回避したり、他者から受け取ったPCBの品質評価を行うことができるように、こちらで役立つガイドをご紹介いたします。
理想的なはんだ接点
はんだの不良を探す場合、比較のために理想的なはんだ接点の画像があると役立ちます。
理想的な挿入実装はんだ接点–良い時のキスらしい
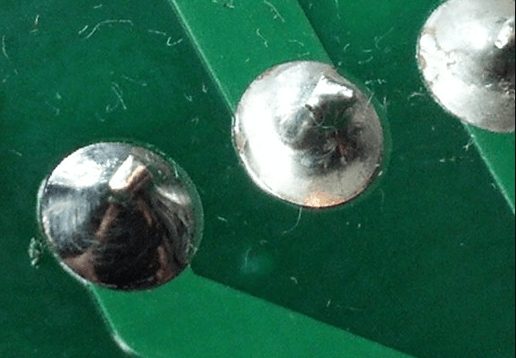
挿入実装部品の理想的なはんだ接合は、「凹面フィレット」であります。これは、水平から40〜70度の角度で滑らかで光沢のある凹面を持ち、良い時のキスのように見えます。はんだごてが適切な温度にあり、PCB接点から酸化物層が取り除かれている場合に実現できます。
理想的な表面実装はんだ接点
同様に、優れたSMDはんだ接点には、滑らかな凹面フィレットもあります。

したがって、優れたはんだ接点の一般的な特性:
–良好で完全な濡れ性
–凹面フィレットがある
–光沢があり、きれい
不良なはんだ接点
残念なのは、不測の事態が発生しやすいですので、PCBに半田投げる品質を著しく低下させます。
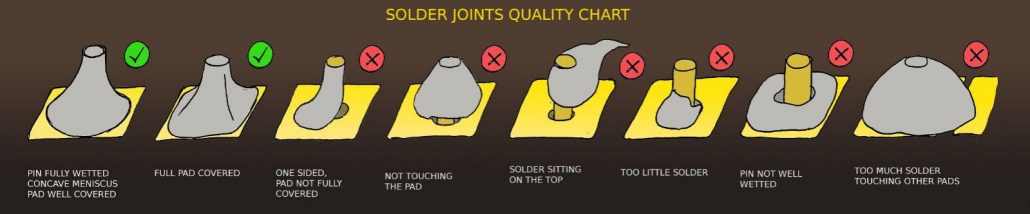
1.はんだブリッジ
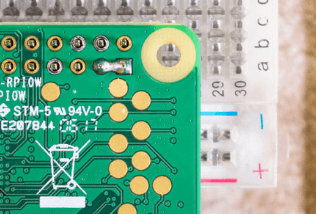
ますます小さな部品によって引き起こされる多くの問題のうち、はんだブリッジがリストの一番上に記載されると思います。それらは2つ以上のはんだ接点が不注意に接続されたときに形成されます。通常、はんだブリッジが発生する原因は、接合部間ではんだが過剰に塗布されたり、大きすぎたり幅広すぎたりするはんだごて先を使用することであります。もしブリッジのサイズはものすごく小さくて、はんだブリッジの認識が困難になります。検出されないままにすると、短絡につながり、部品が焼損する可能性があります。
はんだブリッジを修正するには、はんだごてをブリッジの中央に保持してはんだを溶かし、それを引き抜いてブリッジを破壊します。はんだブリッジが大きすぎる場合、過多のはんだをはんだ吸盤で取り除けば、問題解決できます。
2.過多のはんだ
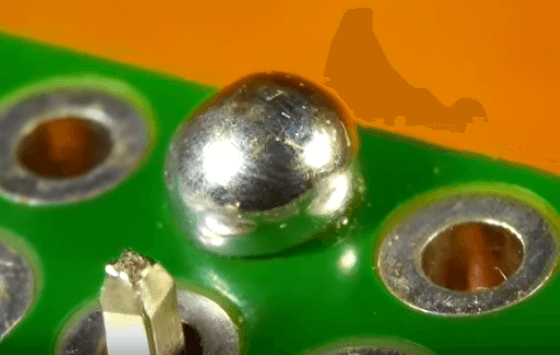
ピンにはんだを付けすぎると、丸みを帯びた形状が特徴の過多のビルドアップが発生します。初心者については、PCBに半田投げる時はんだが多いほど良いと思っていますが、ピンかパッドか適切に濡れていないとはんだブリッジが形成されやすい恐れがありますので、想像される通りにいけません。通常、ピンとパッドを十分に濡らすには、十分なはんだが必要です。また、接合部の濡れにより良くアクセスできるように、最良の凹面も必要です。
3.はんだボール
はんだボールはウェーブまたはリフローはんだ付で発生する最も一般的なはんだ付の不良の1つであります。はんだボールは小さな球体のように見えます。はんだボールは、不適切なソルダーペースト印刷、不十分なリフロー温度設定、不注意でPCB設計、酸化した電子部品の使用などの原因で発生するのは普通です。
4.冷接点
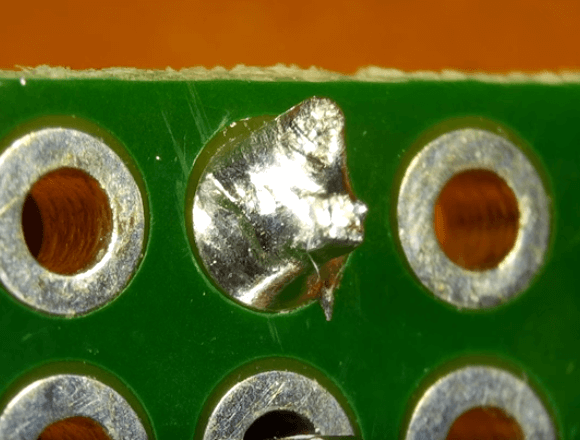
通常、冷接点はブロック状の面としているのは、冷接点をを溶かすための不十分な熱によって引き起こされます。例えば、溶接ガンの加熱時間不足による温度不足も要因の一つです。また、回路自身設計によっても冷接点を生じる可能性があります。例えば、熱緩和を考慮せずにグランド層に直接接続されたパッドは、はんだごての熱がグランド層を流れる恐れがあります。もし液化を拒否する頑固なはんだ接合部を見つけると、設計に問題のある可能性があります。それで、適切な修正されなければ、亀裂は時間が経つにつれて形成され、最終的には失敗に至ります。
5.過熱はんだ接点
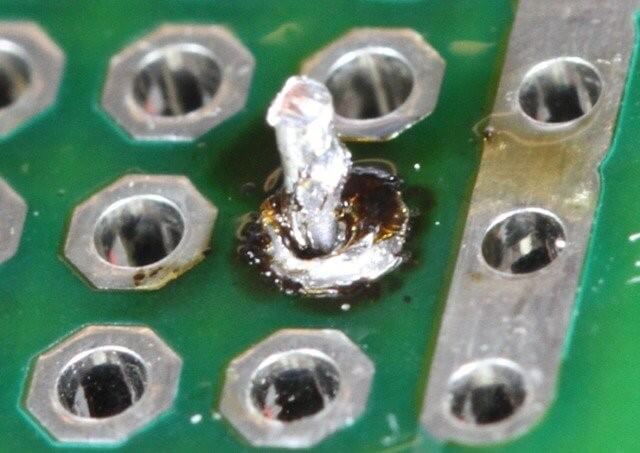
熱が少なすぎると不安定なはんだ接点が発生するように、熱が多すぎるとはんだに影響も与えます。はんだ接合部の過熱の原因はいくつかあります。1.溶接ガンの設定温度が高すぎる2.パッドの表面に酸化層が形成されますので、十分な熱の転写を妨げています。それで、はんだ接点の加熱時間が長くなります。パッドが完全に持ち上がって、ボードが破壊されるか、高価な修理費がかかる場合があります。これを避けるには、溶接ガンの温度の正しく設定して、適切なフラックスを使用することが非常に大切です。
6.ツームストーン
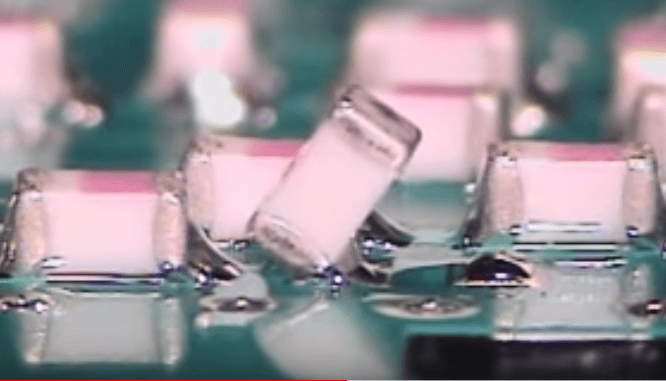
コールドはんだ接続の材料は通常、抵抗器またはコンデンサ静電容量のような表面実装部品です。しかし、材料の片面とパッドの密着性が悪いため、材料の側面が傾いているように見えます。
リフローはんだ付では、一方のパッドのはんだペーストが溶融してから他方のパッドがツームストーンを引き起こす可能性があります。例えば、サーマルリリーフやパッドに接続されたラインの厚さが等しくありません。ウェーブソルダリングでは、入ってくるはんだウェーブによって、物理的に押されて大きな部品になる恐れがあります。そして、部品はツームストーンの形になります。レイアウトエンジニアは、ウェーブはんだ付け用のボードを設計する際に、ウェーブの方向を考慮する必要があります。
7.不十分な濡れ(挿入実装)
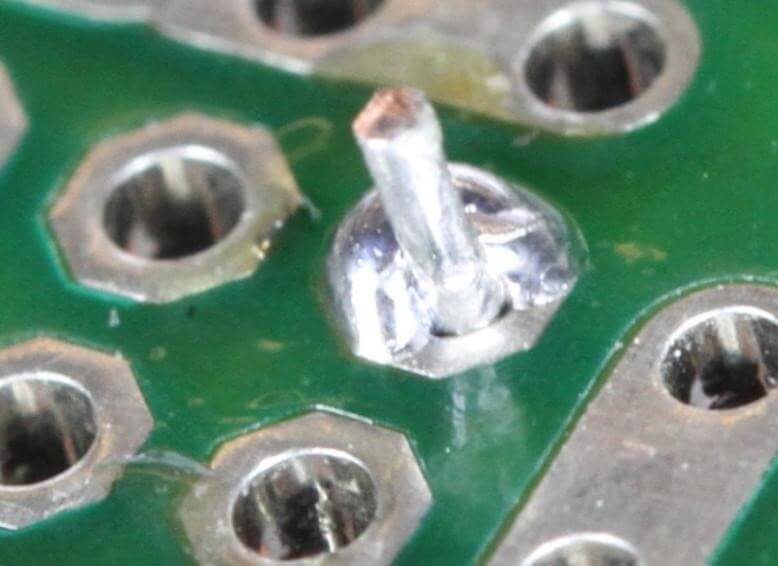
完全に濡れていないはんだ接点は弱いと、ボードとの強力な接続は形成されません。理想的には、パッドとピンではんだが100%濡れ、隙間やスペースが露出しないようにする必要があります。はんだぬれ不良は、ピンとパッドの両方に熱を加えられず、またはんだがフローするのに十分な時間を与えられないことに起因します。ボードが汚れていることが原因の場合もあります。そこで、ボードを完全に洗う、パッドとピンの両方を均等に加熱するのは、修正する方法であります。
8.濡れ不足(表面実装)
右側に3つのピンは完全に濡れていません。
はんだがパッドに流れ込まないように、リードのみを加熱すると、同様に、SMD部品も濡れ不良の影響を受ける可能性があります。上の画像では、SMD部品の3つのピンは、それぞれのパッドで十分に濡れていません。ピンのパッドの代わりにピンが加熱されたため、ピンのはんだはパッドに流れなかったんです。この不足を修正するためには、溶接ガンではんだパッドを加熱し、スズを添えて不足分を補足します。
9.はんだスキップ
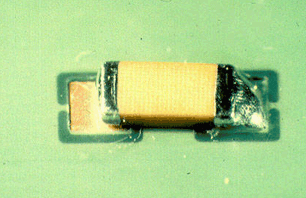
はんだで濡れていないはんだ接点は、一般にはんだスキップと呼ばれます。これは、はんだが表面実装のパッドから飛び越えて、断線になるときに発生します。スリップアップには発生した理由が多くあります。例えば、パッドのサイズが不均一であるか、ウェーブはんだ付けを実行するとき製造者はボードが不適切なウェーブの高さを使用しています。
10.リフトパッド
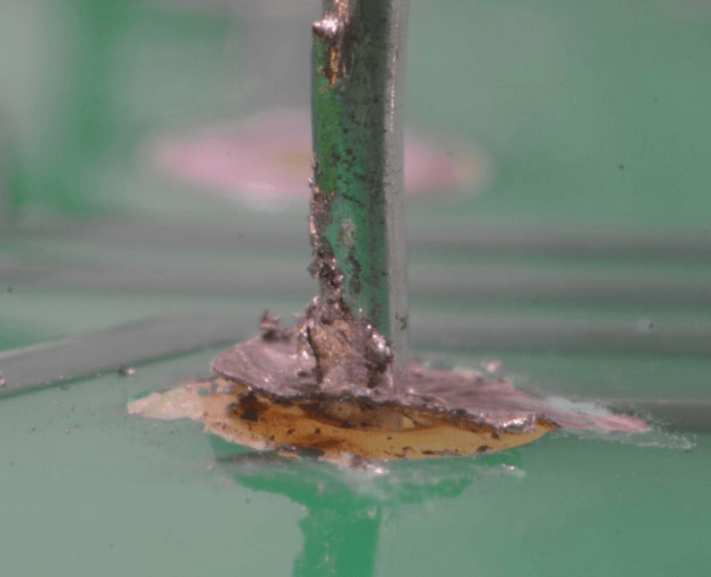
リフトパッドとは、おそらく既にあるはんだ接点への過多の力または過多の熱のために、PCBの表面から分離したはんだパッドであります。このようなパッドは非常に壊れやすく、トレースから簡単に裂ける可能性があるため、使用が困難になります。安いものでしたら、このまま廃棄するのはお勧めです。
11.はんだ不足
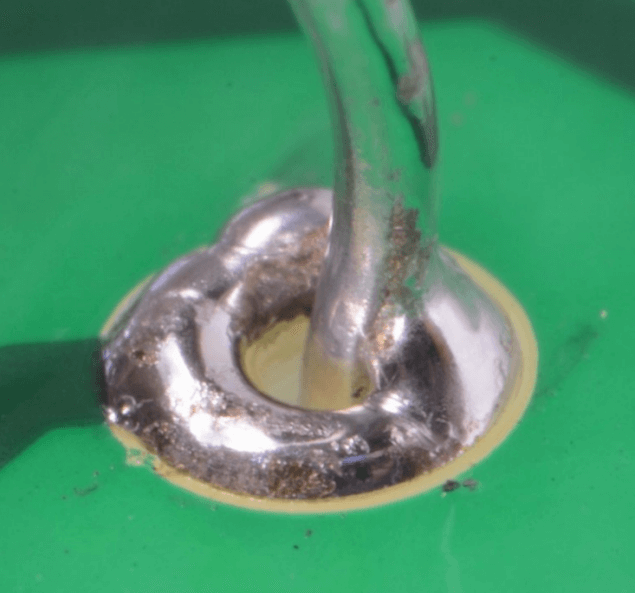
その名前通り、はんだ不足により、しっかりした電気接続を形成するにはできません。それはリードに十分な熱が加えられていないため、不足の接続になるかもしれません。まだ電気接触が行われているうちなので、その不足の接点が機能するという可能性もあります。それにもかかわらず、はんだ不足の接点は、時間の経過とともに亀裂が発達して接点が弱くなるため、最終的には故障する可能性があります。幸いなことに、はんだ不足の接点を救うこと修正することができます。それは接点を再加熱して、はんだ量を増やする方法です。
12.はんだ飛沫/ソルダウェブ
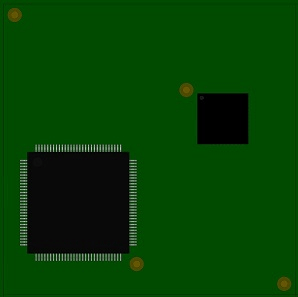
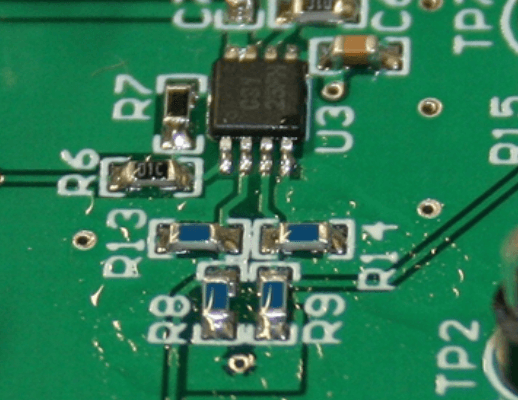
これらのはんだの小片は、乱雑な飛び散りでソルダマスクにくっつき、くもの巣の外観のようになります。これらの不規則な形状の糸は、不十分なフラックス剤の使用またはウェーブソルダリング中のボードにある汚染物質によって引き起こされます。そして、ショートを引き起こす恐れがあります。
13.ピンホールとブローホール
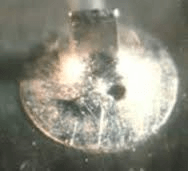
ピンホールとブローホールの不足は、はんだ接点の穴として表示されて認識しやすいです。ピンホールまたはブローホールという用語は、ホールのサイズを示す手がかりになります。ピンホールは小さなホールを指し、ブローホールははるかに大きなホールを指します。
悪い手はんだ付の技術の結果になるのではない、普通はウェーブソルダリンの中にピンホールとブローホールが形成されます。ボード内の水分は、はんだ付工程の中に加熱されてガスになり、そして溶融状態のときにはんだを通して逃げます。それで、はんだ接点が固化したときにガスが逃げ続けると、ボイドが形成されます。この問題を避けるように、ボードを焼くか予熱して水分を除去し、スルーホールに約25umの最小の銅メッキ厚を持たせることという方法はあります。
はんだ付の問題を避けるために何ができるの?
はんだ付の問題を完全に防止する確実な方法はありませんが、はんだ付の問題の発生するリスクを減らすために、PCBの設計およびはんだ付の際に採用できる良策がいくつかあります。
1.ソルダーレジスを考える
普通は緑色で、環境から銅を保護するためにPCBの表面に塗布された薄いポリマーコーティングのソルダマスクです。はんだはコーティングにうまく付着しないため、酸化を防止するだけでなく、はんだブリッジの形成も防止します。したがって、パッド間にはんだマスクを設計して、はんだマスクダムを形成することができます。これはICおよびBGAで特に役立ち、パッド間の隙間をインチまでものすごく小さくすることができます。
2.基準マークを配置する
基準マークは、PCBの設計段階でPCBボードに配置された、基準マークは丸いはんだマスクの開口部であり、その中心に円形の裸銅があります。特別な処理の必要がある部品には、パネル基準マークと個別部品基準マークがあります。ピックプレース機は、それらの基準をPCB上の基準点として、実装中にボードのSMD部品を調整します。正しく使用すると、配置の精度があげられます。同様に、不良の基準マークの設計になる場合(たとえば、不良の配置であるか、不良の基準である場合)、不良の方向付になり、はんだ付の問題のリスクも高まります。
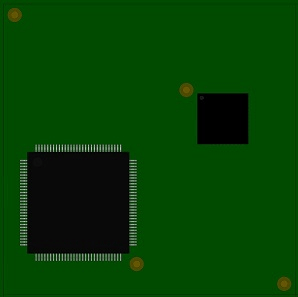
3.はんだごて先の洗いと予備はんだ
はんだごては、初めて使う時から手入れが必要です。これをしないと、ごてに付いている汚染物や酸化物などの物ははんだごて自身の熱伝導能力を低下させ、そしてはんだ接点の品質も低下させます。新しいはんだごても、すぐに使えなくなってしまいます。そのため、はんだ付を始める前に、はんだごて先の清潔に注意してください。基本的には、こて先にいつもはんだが付いた状態にしておきます。 部品などをはんだ付けする時に、こて先をクリーナーで綺麗にしてから、はんだ付けします。 こて先にはんだが残った状態になっていますが、それで OK です。 終了時には、こて先にはんだを少し溶かしてコンセントを抜きます。
それを仕上げしたら、鉄に予備はんだするべきです。はんだごて先の予備はんだは、先端を酸化から保護し、熱を伝導する能力を向上させるために、先端をはんだの層でコーティングするということです。2つまたは3つの接点をはんだした後、はんだごて先をクリーニングして、その都度はんだが終わった後にもう一度洗浄します。このようにすることで、はんだごての使用寿命を延長することができ、はんだ接点の品質を改善することもできます。
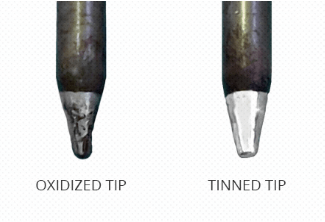
4.練習で完璧に
はんだ付は、練習すればするほど良くなるスキルです。古い回路基板またははんだ付の練習用のボードで好きなだけ練習してから、はんだ付けは上手になります。さまざまな手法を試してみて、はんだごてが手にぴったり合う方法を見つけ、はんだとチップを所定の位置に保持する時間を測定し、多くの間違いを犯します。
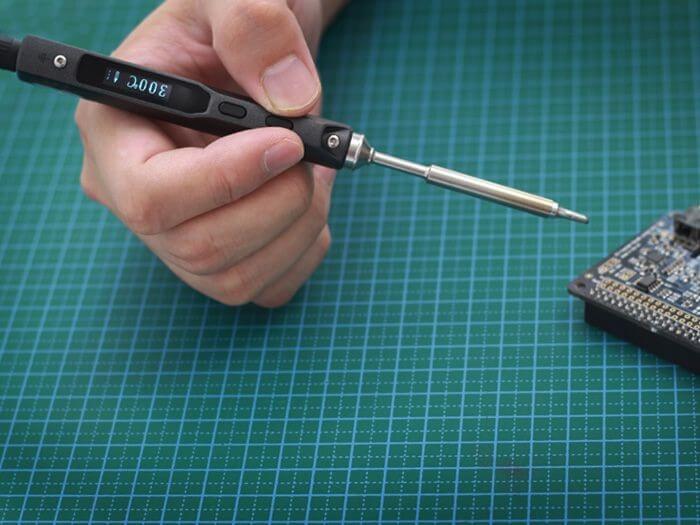
5.適切なPCB実装者を選択する
一人で部品の手はんだ付と調達が面倒な場合、または小さな部品で作業することができない場合は、経験豊富なプロのPCB実装者をご選択になることがよくあります。
10年の業界経験により、SeeedのFusion PCB Assembly(PCBA)サービスは迅速に部品を調達し、完全な回路基板を組み立てることができます。
これは今弊社が持っているものです。非常にひどいはんだ接点を共有していただければ喜んでいます。以下のコメント部分でそれを共有しましょう。