部品実装プロセスを行う開発者にとって、電子部品の種類だけでなく、品質も、部品の選択に非常に重要です。これは電子部品の調達先にも関連しています。 Seeed Fusion部品実装サービスには、信頼できる電子部品の販売代理店がサポートしているため、多くの在庫と品質の高い部品があります。 これから紹介します。 Digikey Digi-Keyは、アメリカ合衆国ミネソタ州に本拠を構える電子部品の通信販売を行う企業で、世界で5番目に大きな電子部品の販売代理店です。 2015年Digi-Keyと協力して以来、在庫は十分で、品質も保証されており、部品を購入することが保証されています。 Mouser Mouserは、670を超えるメーカーからの400万点以上の製品を揃えており、即日出荷可能在庫は74万点以上の米国大手半導体・電子部品商社です。 Mouserはエンジニアやバイヤーのために新しい製品や技術を急速に導入することに取り組みます。足りる在庫と品質保証は、私たちが提携する理由です。 Element14 Element14は電子システムの設計、維持および修理を担当する高いサービス販売業者です。ある特別な部品はElement14から調達できます。の収集、バイヤー、エンジニアに結びついた製品、Element14は製品、サービス、最新のソフトウェアの開発をすべてオンラインコミュニティプロジェクトに接続しますので、バイヤーやエンジニアはそれを通じて、 同輩や専門家と近づいて、幅広い強固な技術情報や有用なツールを入手できます。 新技術の研究、電子製品の設計、既存のシステムを修復するための部品の探しなどもできます。 Particle Particleは、企業が接続ソリューションを迅速かつ簡単に構築、接続、および管理できるようにする、拡張性と信頼性の高いネットワーキングデバイスプラットフォームです。 Kickstarterで2013年を開始し、インターネット企業にとってシンプルで便利なものにしました。最近 Seeed FusionはParticleの強力なP0およびP1 Wi-Fiモジュールを当社のOPLに統合しました。 もちろん、それらの部品調達先は、弊社の必要とするすべての部品を満たす訳ではないので、深センの地元部品メーカーと協力しています。部品を得るために、彼らは多くの専門ルートを提供しています。Seeedの部品ライブラリと組み合わせて、Fusion PCB 部品実装サービスは ワンストップで高品質、手頃な価格のサービスを提供しています。
詳しくへCategory: お知らせ
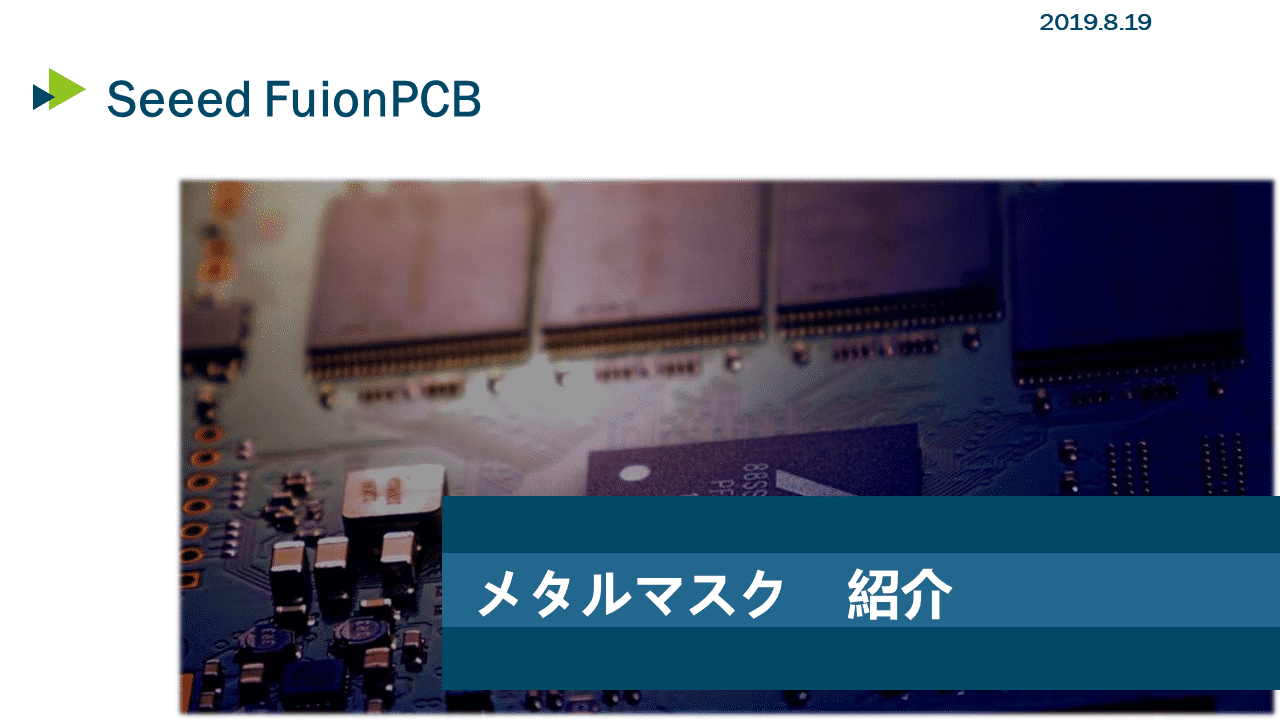
メタルマスクとは?-プリント基板の実装品質を左右する
2019.8.19追記更新—— PPT画像追加 メタルマスクとは メタルマスク(ステンシル)は、プリント基板製造工程のひとつである表面実装において、プリント基板上にハンダペーストを印刷する際に用いられる治具です。主に厚さ0.2mm以下の非常に薄いステンレス板に微細な切り欠きパターンを作り、ここにハンダペーストを刷り込むことによりプリント基板全体の部品装着部にハンダパターンを形成します。 その製造方法の1つとしてレーザ加工法があります。 メタルマスク製造解説 from ssuser97ba8f これ以外にもエッチング法、アディティブ法(メッキ法)があります。当社のレーザ・ステンシル加工機は、この切り欠きパターンをレーザ切断により形成する専用加工システムです。 レーザ加工法はドライプロセスであるため環境にやさしく、より高速で、高精度のメタルマスクを製造することが可能です。またエッチング法やアディティブ法に比べて環境面に加えコスト面、納期面でのメリットがあります。 メタルマスク製造解説 from ssuser97ba8f メタルマスクの役割 プリント基板には抵抗やコンデンサ、マイコン等の様々な電子部品がハンダ付けによって取り付けられています。しかし一つのプリント基板にはこれらの小型部品が数えきれないほど取り付けられています。しかし何百個もある、それも小型の電子部品のハンダ付けを手作業で行うと、膨大な時間を要してしまいます。また、あらかじめどこに何を取り付けるのかが決まっているため、手作業で行うと、ハンダ付けの失敗や取り付け場所の間違い等の問題が発生してしまいます。そこで登場するのが「メタルマスク」です。 それが何百枚、何千枚と作られている訳ですが、一体どの様にしてハンダ付けは行われているのでしょうか。 まずはメタルマスクとプリント基板を重ねます。クリーム状のハンダを流し込み、スキージと呼ばれるヘラで刷り込みます。そしてメタルマスクを取り除くと、必要な所にだけハンダが印刷されることになります。専用機械(実装機械)によって電子部品をハンダ上に配置し、熱風(リフロー炉)によって、ハンダを溶かしてプリント基板と電子部品をプリント基板の表側で接続します。 このようなプリント実装基板の工法を表面実装と呼び、これにより生産効率や歩留まりが劇的に向上してきているのです。この工法において、メタルマスクはなくてはならない役割を果たしているのです。近年の電化製品の小型化、高性能化は、これら技術をより高度化した数々の工法により成り立っているのです。 格安メタルマスク製造サービス メタルマスク製造解説 from ssuser97ba8f 表面実装技術の身につけを容易にし、小ロット生産を支援するために、Seeed Fusionは今月からメタルマスクの値段を下げしました。 精密できれいなエッジを確保するために、Fusionのメタルマスク製造サービスでは、頑丈な304ステンレス鋼を使用し、最新鋭のレーザー加工機による高精度高品質のメタルマスクをご提供しております。 すべてのサイズは、わずか9.90ドルから始まり、最大サイズの場合、元価格の3分の1になります!メタルマスクの仕様と価格はここでご覧ください。 サイトで自動見積り計算される 日本語サポートたっぷり 24時間内製造完了…
詳しくへメッキミシン目(スリット)を設計する方法
Seeed Studio Fusionの場合、製造ファイルでメッキミシン目(スリット)の作る方法は、メッキスルーホール(PTH)に似ています。 つまり、何らかの種類の穴、銅めっき、および銅を露出させるための開口部がなければなりません。 次の簡単な手順でこれを行う方法を示します: 1.ご利用の設計ソフトウェアで、メカニカルレイヤー(GMLまたはGKO)にミシン目(スリット)のアウトラインを描きます。これはメッキ後の穴の最終サイズになります。 正確な寸法を確保するために、アウトラインは基板のアウトラインと同じように、ゼロ幅の線を使用して描画する必要があります(小さな切り抜きのように見えます)。 形状の内側の領域のみが切り取られます。 2.両面の銅箔パッタンレイヤ(GTL、GBLおよびその他の銅箔パッタンレイヤ)で、同じミシン目(スリット)を描きますが、メカニカルレイヤのスリットよりも少なくとも0.1 mm(約4mil)大きくします。 露出される銅箔の量はご自分の次第です。 3.最後に、ソルダレジストレイヤ(表面と裏面)にミシン目(スリット)開口部を引き、銅パッドよりも少なくとも0.16mm(約6mil)大きくします。 4.他の銅箔パッタンレイヤとソルダレジストレイヤにもこの作業を行うことを忘れないでください。そうすると、メッキミシン目(スリット)を設計しました。 メッキミシン目(スリット)とメッキスルーホールとの違いは、切り抜きの形状です。 通常、NCドリルレイヤにドリルヒットでPTHを示します。 メッキスロットの場合、開口部を切り欠きとして描きます。 一部のコンポーネントライブラリでは、個別のNCミリングレイヤにメッキスロットが生成されますが、NCミリングレイヤをCAMソフトウェアに正しく読み込むことは困難な場合がありますので、推奨しません。 また、塗りつぶされた図形として設計されている場合もありますが、当社のエンジニアは図形の正確な寸法に従わない場合がありますから、ゼロ幅のアウトラインを使用することをお勧めします。 当社の最小のミリング工具は直径0.8mmですので、これよりも小さいミシン目(スリット)が必要な場合は、ドリル穴を重ねて列として設計し、それらをNCドリルレイヤに入れてください。
詳しくへ高度なパターン設計にも迅速に対応できるAdvanced PCBサービスがスタート!
今回はFusionの「Advanced PCB」という特注基板製造サービスを紹介させていただきたいと思います。 Advanced PCBサービスは50層までの基板、10ozまでの銅箔、特殊ビア(マイクロビア、プラグ付きビア、貫通樹脂埋めビアなど)、高密度相互に連結する基板などの高度設計に対応できます。標準製造サービスにない表面仕上げ(OSP、Hard Gold+ENIGEなど)、インピーダンス制御、細いパターンなどの高度な機能が利用可能になります。最高仕様の加工能力と特別対応があるため、標準基板と比べると、数倍の価格になります。詳しい仕様違いをここでご覧ください。 豊富的な製造経験、合理的な価格、保障ありの品質、Fusion Advanced PCBサービスは理想的な選択です。 特注基板の必要がございましたら、ぜひFusion Advanced PCBサービスをご利用ください!
詳しくへ基板設計ガイド – 高品質でレイアウトする方法
プリント基板の設計は、すべての電子回路設計の基礎です。 回路にあるすべての部品を装備する主なキャリアとして、 プリント基板は、散乱した部品の組み合わせだけでなく、回路設計が確実であることを保証し、異なるワイヤを接続する際の人為的ミスを回避するためにも使用されます。 1.パターンは合理的な方向にある必要がある 例えば、入力/出力、AC / DC、強/弱信号、高周波/低周波、高/低電圧などです。 それらの方向は線形(または別々)であり、交差して相互干渉ではありません。 最良の方向は直線ですが、達成するのは難しいです。 最も不利な方向はリング状です。 DC、小信号、低電圧の基板設計では、要件はあまり厳しくない場合があります。 合理的なのは相対的なものです。 2.良い接地を選択する 接地点は何回も言及されています。普通には、メイン接地点が必要です。例えば、フロント増幅器の接地パターンを合併してから、メイン接地点に接続します。 制限があるため、達成するのが難しい場合もあります。 実際には鋭い問題です。 エンジニアには独自の解決策があります。 3.電源フィルタ/バイパスコンデンサを適切にレイアウトする 一般に、回路図にいくつかの電源フィルタ/バイパスコンデンサを配置しますが、どこに配置するべきかは示されていません。 これらのコンデンサは、濾過/分離される必要なスイッチ装置や他の部品に使用されます。レイアウト時、ンデンサは、これらの部品の近くに配置すべきです。そうでなければ効果がありません。 また、電源フィルタ/バイパスコンデンサを適切にレイアウトすると、接地点の問題はやすくなります。 4.パターン幅はブラインドビアとスールホールにも適切である 太いパターンを使うなら、細かいパターンを使わないでください。高電圧と高周波数のパターンは滑らかで角度はありません。 アース線はできるだけ広げなければなりません。最良の方法は銅注ぎです。 パッドとビアが小さすぎると、パッドを「c」または完全にカットするのとドリルが難しくなります。パターンが細くて、銅が注がれない場合、パターンのエッチングの品質は悪化します。 だから、銅の注ぎは、接地での使用だけでなく、生産にも役立ちます。 5.ビアの数とパターンの密度を適当にする 製造の初期段階に見つけない問題は後半に出現する傾向があります。 例えば、パターンとビアが多すぎると、銅のエッチングの時には危険です。 したがって、ビアのデザインを最小限に抑える必要があります。…
詳しくへプリント基板のソルダレジストの色について
一般的にプリント基板は真緑色と認知されていると思いますが、あれは基板の色ではなく、塗布されているソルダレジストの色です。ソルダーレジストはプリント基板の表面に塗布し、絶縁膜となる保護インキです。実装の際にはんだが不必要な部分へ付着してショートするのを防止する役割があります。また、ほこりや熱、湿気などから回路パターンを保護し、絶縁性を維持します。 上記の機能の為だけであれば、ソルダーレジストの色が特に問題になる事はなく、レジストは緑、シルク文字は白というのが最も一般的で、製造コストや納期にも有利なのですが、最近は色々な理由から、他の色での要望も増えているようです。 ではなぜ、黄、赤、黒、白など、カラフルなソルダレジストを使う必要があるのでしょうか。いくつかの理由があるようです。 (1)LOTやバージョンで色を使い分ける たとえば、1回目の試作は赤、2回目は黄色、そして製品となったら緑色を使用するなど、開発段階が一目でわかるように色分けを行う場合があります。 (2)実装する部品によって使い分ける ピカピカと光るLEDを実装する場合、より美しく光らせるために、黒色のソルダレジストを使う場合があります。夜空に咲く花火のイメージです。その反対に、受光素子が実装される基板には、乱反射を避けるために、白色のソルダレジストを使用することがあります。 (3)その時の気分や、好き嫌いで決める 「気合を入れるために、赤にしよう」「今日は暑いから、涼しげな青にしよう」など、気分で色を使い分ける場合もあるようです。単に、開発者の好きな色を使用する場合もあります。完全に個人的な趣味です。特にアメリカではこの理由が多いと聞きます。 それでは、異なるソルダレジストの色はプリント基板に何か影響がありますか? 色によって基板の特性の違いはほぼありませんが、半製品の生産の容易さに影響あります。例えば、 配線とシルクのチェック、回路の見分けなどです。 異なるソルダレジストの色のメリットとデメリット 緑 プリント基板の色はなぜいつも緑ですか? 1. SMTはんだ付けには、AOIチェックがあります。このプロセスにあるアラインメントの光学較正と計測器の認識にとって、緑は優れています。 2. 他より、緑はコスト低く、エラーを少なくし、より高い精度で行うことができます。 3. 緑は環境に優しいです。 黒 黒色はコバルトと炭素とが混ざり合っているもので、ある程度の導電性があるため、短絡の危険性があります。 黒い基板は回路を見にくく、価格も安くありません。 白 ほとんどのLED照明は白い基板を使ってます。Seeedは白い基板上の黒色のシルクを印刷し、高級感に見せます。 青 青はLCDを搭載するのに適した色です。明るい背景色と鮮明に対照的な縁によって、目が画面から引き出されないからです。青は基板をきれいに見せます。 赤と黄 赤と黄は欠点ありません。 実際、それは緑と同じので、見事なパターンがあるならば、ご基板は芸術作品のようになります。 基板が4層以下、寸法≤…
詳しくへガーバーデータとは
ガーバーデータとは、プリント基板(Printed Circuit Board, PCB)の設計・製造過程で使用されるファイルフォーマットの一種です。「ガーバー」「ガーバーデータ」「ガーバーフォーマット」など色々な呼び方があるが、どれも意味としては同じです。ガーバーデータには基板の配線情報などが含まれており、 通常DesignSparkPCBやEagleといったのCADソフトによって設計・出力され、このファイルを元に製造業者側はプリント基板を製造します。 作成されたファイルは、基板製造のCAM システムに読み込まれ、基板製造プロセスの各ステップで使用するデータに編集されます。また、基板の加工以外にも、基板の仕上がりを検査する自動外観検査機にも使用されます。ドリル情報(フラッシュアパーチャなど)に使うことも考えられるが、通常、ドリル情報はExcellonフォーマットが使用されます。 ファイル構造の視点からみると、ガーバーフォーマットは、RS-274X(拡張ガーバーフォーマット)とRS-274-D(標準ガーバーフォーマット)の2つに分類することができます。 2種類の形式があり違いは下記のようにDコード(アパーチャー・リスト)を含むか含まないかの違いです。 Dコードを含まないデータ・・・RS-274D(標準ガーバー) Dコードを含むデータ ・・・RS-274X(拡張ガーバー) 注)Dコード・・・サイズ情報(ポイント寸法、線幅)・形状を示すコードで2桁以上の数値 簡単に言ってしまうと、RS-274Xは画像データを全て内包することができ、外部ファイルを必要としません。逆にRS-274-Dは、サイズ情報が記述された外部ファイルが必要になります。そのため、RS-274Dは正しい組合せでファイルを受け渡しをしないと、正しく再現出来なくなってしまいます。当然のことながら、現在の主流は拡張ガーバーです。 見分け方は簡単で、RS-274Xの場合、先頭付近に「%」で区切られたパラメーターが何行か並んでいるはずです。 このパラメーターがない場合は、RS-274-Dですので外部ファイルが必要になります。 RS-274Xでの受け渡しはトラブルが少なく、ガーバーの知識がさして必要ではありません。一方、RS-274-Dを使う場合は、正しくデータを再現するために設計者と正常者双方に正しい知識が必要になります。 Fusion pcbの場合、ガーバーファイルはRS-274Xフォーマットでなければなりません。 ドリルファイル(pcbname.TXT)はExcellonフォーマットである必要があります。
詳しくへ日本のメイカースペース【DMM.make AKIBA】との協力がスタート!
8月3日、Seeed Fusionチームは日本ロレアルリサーチ&イノベーションセンター、日本を代表するモノづくり支援施設DMM.make AKIBAを見学させていただき、DMM.make AKIBAと協力体制を築いていくことで合意しました。 まずは支援の一環として、Maker Faire Tokyo 2017で配布した「製造のためのプリント基板設計ガイド」を特別にご用意し、DMM.make AKIBAで無料配布いたします!DMM.make AKIBAの会員さまはもちろん、少しでも興味をお持ちの方はこの機会に無料見学ツアーやワークショップにご参加いただき、この貴重なガイドをご入手ください。DMM.make AKIBAでモノづくりの楽しさを体験しよう! 【DMM.make AKIBA】との協力を推進し、モノづくりを支えます。次にご期待ください!
詳しくへ回路基板を設計する方法
初心者にとって、回路基板の設計方法をにつけるのは素晴らしいことです。 ここでは、7つの過程をまとめて、回路基板の設計方法に関する大まかな概念を理解するのに役立つと思います。 1.事前設計 事前設計には、コンポライブラリと回路図を準備しておきます。基板設計を進める前に、回路図のSCHコンポライブラリと基板のコンポパッケージを準備する必要があります。 エンジニアから標準サイズのライブラリを設計する方が良いです。 一般的には、基板コンポパッケージライブラリを確立した後、SCHコンポーネントライブラリを確立します。 基板コンポのパッケージライブラリは、基板実装に直接影響を与えるため、厳しい条件があります。 独自のライブラリを作成するより、コンポが在庫あるライブラリを利用する方がいいです。 Seeed Fusionのように、部品リストとEagleライブラリとKicadライブラリを提供するので、プロセスが簡単になります。 回路図のSCHコンポライブラリの条件は比較的に緩いですが、ピン特性の定義と基板コンポパッケージライブラリの対応に注意してください。 事前設計を完成して、次の6ステップを続きたくない場合は、FusionレイアウトサービスページでSCHをアップロードして、設計にかかる費用が即時に出てきます。(生産の準備ができている設計) 2. 基板の構造設計 基板のサイズと機械的な位置に応じて、基板設計環境で基板の枠を引き出し、必要なコネクタ、ボタン/スイッチ、ネジ穴、実装穴などを位置決め要件に従って配置します。 配線領域と非配線領域(非配線領域の周囲のネジ穴の範囲など)を十分に検討して決定します。 3. PCBレイアウト設計 レイアウト設計では、基板の枠の設計要件に従ってコンポを配置します。回路図ツールでネットワークテーブル(設計→ネットリスト作成)を作成して、ネットワークテーブル(設計→インポートネットリスト)をPCBソフトウェアにインポートします。その後、ネットワークテーブルはソフトウェアの背景に存在し、配置操作によって接続できるライン候補間のすべてのコンポおよびピンを呼び出すことができ、次にコンポに基づいてレイアウト設計を行うことができます。 PCBレイアウト設計は、基板設計プロセスの最初の重要なプロセスであり、基板が複雑になればなるほど、後の配線を実現するための難易度に直接影響するため、より良いレイアウトが要求されます。 レイアウト設計は、回路設計者の基礎と豊富な設計経験に依存しているため、回路設計者に厳しい条件があります。首位の回路設計者は、小型モジュールレイアウト設計または難解なPCBレイアウト設計に適しています。 4. 基板配線設計 配線設計は基板設計プロセスで最大の作業負荷を持ち、PCB基板の性能に直接影響します。 PCB設計プロセスでは、配線には一般に3つの部分があります。まずはクロスパスで、回路基板設計の基本です。 次は標準的な基板の測定である電気性能の表現です。配線後、電気性能が最もよくなるため配線を調整します。 最後はきれいで美しいです。混沌とした配線は、電気性能が許容可能であっても、後の改善やテストやメンテナンスに不便をもたらします。 5.レイアウトとシルクの改善 “もっと優れた基板設計があります”、 “基板設計は欠陥のある芸術品です”、これは主に基板設計がハードウェア設計の要件を満たす必要があるからです。ただし、特定の要件の間に異なる競合が存在する可能性があります。…
詳しくへMaker Faire Tokyo 2017
Maker Faire Tokyo 2017は順調に終わりました。FusionチームはMaker Faireに出展したのは初めてなので、たくさんのご来場ありがとうございました。今回多くのFusionユーザーと出会って、すごく楽しかったです。 多くのユーザーはFusionのプリント基板で自分のものを作って、Maker Faireにご出展になりました。 また、今回は多くの「製造のためのプリント基板設計ガイド」を用意したので、皆さんはお気に入るかなぁと心配していたが、意外にすごく人気があります!良かったです! この機会で、このガイドを翻訳いただいた「ツール・ラボ」の佐倉正幸と会いました。協力いただいて本当に感謝しています。 ご来場の皆さんはいろいろご意見やアドバイスをいただき、Fusionチームにとっては貴重なものです。これからよりよいサービスを提供するように努力します!今後とも宜しくお願いします!
詳しくへ